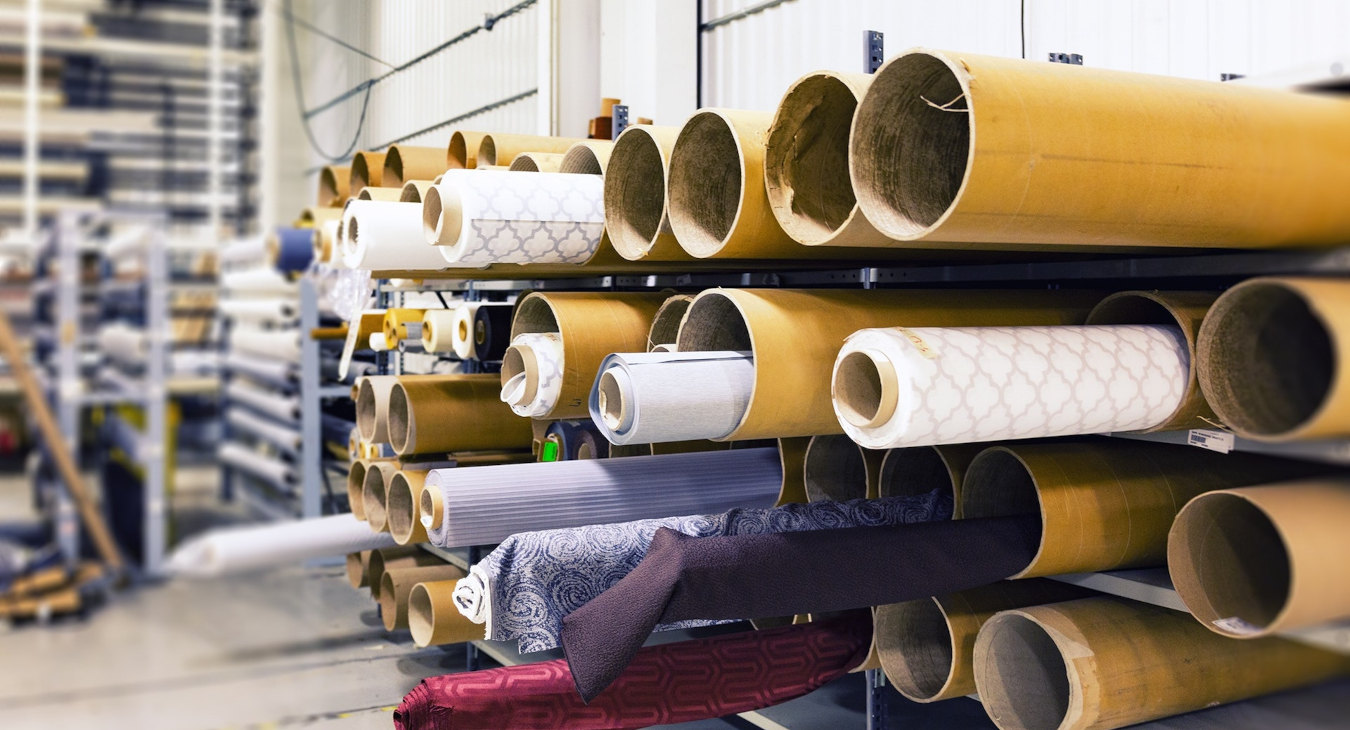
With an annual output of £183 billion, manufacturing is one of the largest operating sectors in the world.
It is also a highly unique industry that requires increased attention from an accounting perspective. While most traditional companies sell stock or services, only manufacturers create their products from the ground up.
Organisations operating in this field have to carefully calculate their raw materials and processing cost to estimate the accurate value of their completed product.
In the following article, we will discuss how accounting for manufacturing differs from mainstream applications and share best practices for success.
How is Manufacturing Accounting Different?
One of the main focuses of accounting services for manufacturing is cost accounting which can be very complex when not handled accurately. Effective cost management allows you to track production costs and extract information that can be used for informed business decisions.
Compared to traditional practices, the manufacturing industry emphasises internal analysis over financial statements for external parties. This data can then be used to calculate production costs for every step of the process.
Carefully gathered financial information can help companies to identify bottlenecks in their manufacturing and increase efficiency. By calculating marginal profitability, accountants can help business leaders identify the most lucrative products and channels to maximise revenue.
In addition to this, manufacturing involves an increased amount of inventory management as tracking costs and cash flow has an even higher significance in this field.
Best Practices for Manufacturing Accounting
1. Consider Your Costing Methods
As manufacturing is a very competitive industry, you must select the correct costing method that fits your business and can help you reach increased profitability. Cost accounting needs to analyse a selection of focus areas such as production costs, capital equipment, labour, and overhead costs.
With the rising cost of raw materials, these outgoings need to be minimised as much as possible while retaining a high-quality product to keep loyal customers and attract new ones.
Due to traditionally long lead and shipment time for parts and products, manufacturing businesses can often find themselves with large accounts receivable and account payable balances regularly. You must keep track of consumer invoice payments from a cash flow perspective to avoid delays.
2. Focus on Inventory Control
Inventory management is one of the most important elements of manufacturing accounting. Typically, manufacturers handle a variety of materials, goods, and final products that you must carefully monitor.
As most organisations in this field will produce a wide range of items, business leaders must work out the cost of their products and maximise their revenue. In recent years, approximately $1.1 trillion of cash was tied up in unmoved stock, so poorly managed inventory can break your financial budget quickly.
Running into regular shortage issues or having a significant excess inventory can negatively affect your profitability and speed of production. It can cause added costs such as storage or cause reputation damage in the long term. With insufficient stock, you can also miss out on opportunities that could expand your business.
In addition to effective inventory management, organisations should look into how they could shorten production cycles to the finished product so they can get their items to their customers faster without storing them for an extended period.
3. Create an In-depth Analysis of Your Manufacturing Process
Once you have effective accounting practices in place, the best way to improve your production methods is to create a thorough financial report. A financial analysis can be instrumental in the manufacturing field.
Besides the obvious benefits of financial planning and tax reports, financial analysis can also help you to see how well your company is running and identify areas for development. 54% of business leaders use business analysis for their decision-making; however, due to unprecedented data volume growth, it is increasingly difficult to keep up with this demand internally.
4. Have a Clear Line of Communication
Another significant challenge in the manufacturing field is the complex nature of the business. Your accounting experts need to communicate with other parts of your business effectively so they can explain their analysis and make suggestions.
Without smooth and fast communication, your accounting function will not be able to reach its true potential.
5. Invest in Expertise
The accounting process for manufacturing businesses can be much more complicated than in other industries due to the complexity of their operations and longer-than-average timelines. Manufacturing procedures also require specific equations that might not be common knowledge for most financial professionals.
External financial partners with years of expertise in manufacturing can add value to your business and help you manage your accounts remotely without incurring labour or training costs. Through external accounting, you can access the most skilled individuals with specific knowledge of your field.
6. Use The Right Accounting Software
Last but not least is the accounting software that you utilise (or not yet!) in your manufacturing business. Automated and cloud-based accounting solutions have been growing in popularity across different sectors, with global spending on cloud-based services expected to reach $397 billion by the end of 2022.
So, if you are still relying on inefficient accounting practices or using legacy systems in manufacturing that result in siloed data, you must definitely tap into the potential of cloud-based accounting tools.
To successfully navigate the manufacturing industry, you must leverage the right accounting software for your business. With the wide variety of software solutions available, deciding which tool is the right one for your business can be challenging.
Nevertheless, cloud-based solutions offer the most streamlined option, allowing you to connect your internal system virtually and sync live data anywhere. Moreover, cloud software can limit system and data problems arising from offline networks and data centres.
The Fine Print
As illustrated, navigating the manufacturing industry requires a specific skill set and a thorough understanding of the best accounting practices, including complex calculations, cash flow, and inventory management.
While keeping track of these necessities can be time-consuming and complicated, external financial partners like Sanay can help you stay ahead of financial challenges and boost your profit.
Read more articles
- Log in to post comments