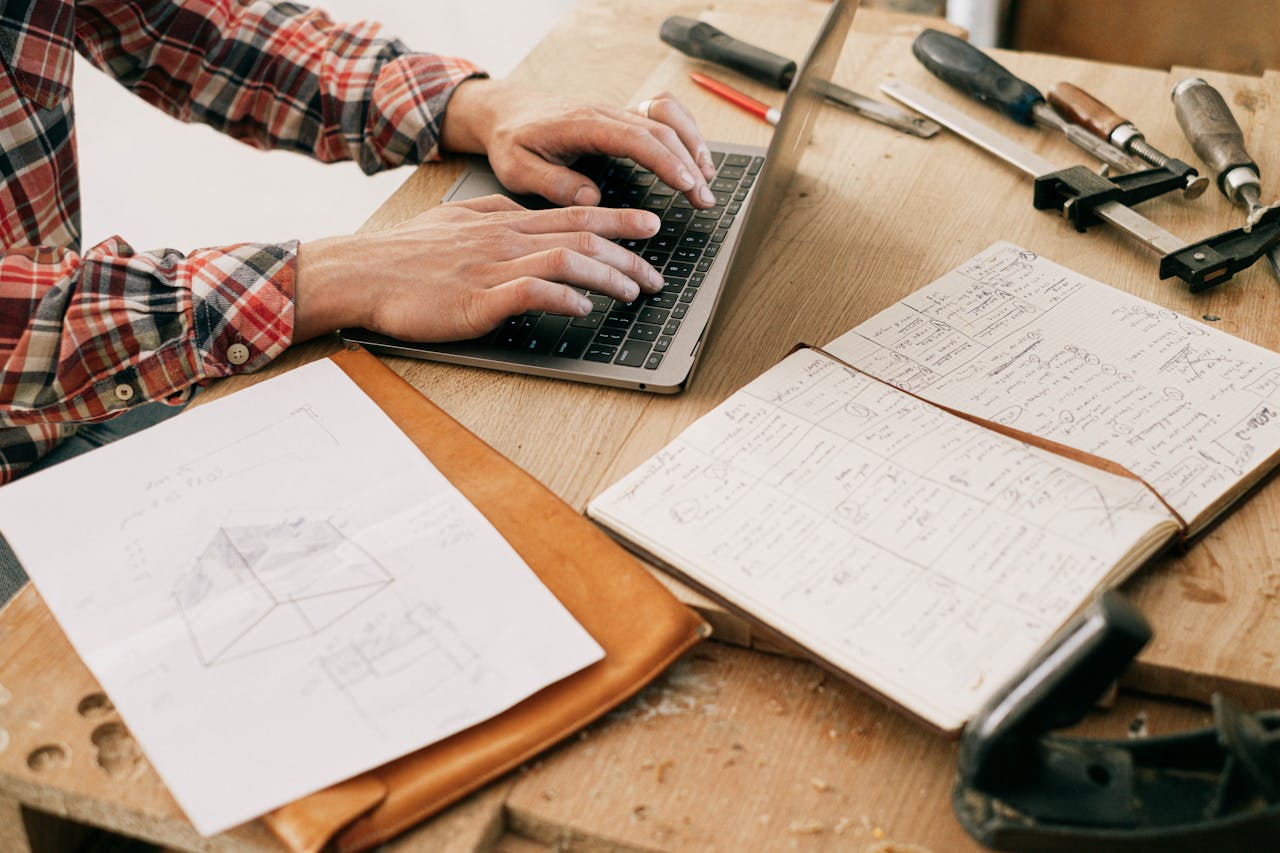
For UK manufacturing businesses, reducing costs is not just about cutting corners but about making strategic decisions that enhance efficiency and productivity.
Nowadays, managing costs has become a top priority for businesses, particularly with the pressure of rising energy prices and fluctuating raw material costs. As these pressures intensify, finding efficient ways to cut costs while sustaining high levels of productivity and quality has never been more important.
This blog explores four specific strategies that manufacturing companies in the UK can employ to achieve significant cost savings.
1. Enhancing Energy Efficiency
Investing in energy-efficient technologies and practices can significantly lower energy bills, providing immediate and long-term savings, particularly as energy prices in the UK continue to exceed pre-Covid levels.
Roughly 48% of companies have seen their profit margins decline due to rising costs, with raw materials being the most affected areas, at 43%.
British manufacturers can start by conducting an energy audit to identify areas where energy is being wasted and where improvements can be made. Simple changes, such as installing programmable thermostats, and maintaining equipment to ensure it operates efficiently, can lead to substantial savings.
2. Investing in Automation and Advanced Technologies
Adopting Industry 4.0 technologies such as robotics and artificial intelligence (AI) can provide significant cost savings over time. A 2024 Forbes Advisor report found that 53% of respondents use AI for task optimisation, while 51% use it for process automation.
By automating repetitive and time-consuming tasks, businesses can increase productivity, reduce labour costs, and minimise human error.
A practical example of this can be seen in a case study from the 2024 MHI Annual Industry Report. A global specialty materials company implemented an AI assistant to aid workers in their daily tasks. This AI tool streamlined learning processes by delivering relevant data and coaching, leading to a 15% improvement in operational efficiency and a 20% boost in productivity.
3. Optimising the Supply Chain
Another area where businesses often encounter cost inefficiencies is in the supply chain, often due to less-than-ideal terms negotiated long ago with suppliers. By fostering strong relationships with suppliers, companies can (and should) negotiate more favourable terms, ensure a steady supply of materials, and minimise the risk of disruptions.
Moreover, implementing just-in-time (JIT) inventory systems can lead to significant cost savings by minimising the need to hold large amounts of inventory, which ties up capital and increases storage costs.
4. Investing in Employee Training and Development
While it may seem counterintuitive, investing in employee training and development can actually help reduce costs in the long run.
A well-trained workforce is more efficient, makes fewer mistakes, and is better equipped to handle new technologies and processes, increasing productivity and reducing waste, both of which contribute to lower operational costs.
With ongoing training, businesses can ensure that their employees are up-to-date with the latest manufacturing techniques and best practices.
The Final Word
If you’re looking to implement these cost-reduction strategies and need expert financial guidance, Sanay can help.
Our team of experienced accountants specialises in supporting manufacturing businesses just like yours. We can help with everything from cash flow management and credit control to R&D tax relief and more.
Get in touch with us today to find out how we can help you streamline your operations and achieve lasting cost savings with our full range of specialist services.
Read more articles
- Log in to post comments